САМОДЕЛЬНЫЕ РАДИАТОРЫ
Для длительной надежной работы мощных полупроводниковых приборов необходимо применять теплоотводы (радиаторы). Самый простой радиатор выполняют в виде плоской прямоугольной или круглой пластины из металла с . хорошей теплопроводностью (рис. 46,а). Такие радиаторы занимают слишком много места, поэтому чаще применяют более эффективные объемные конструкции.
Радиатор-звездочку (рис. 46,6) изготавливают следующим образом. Из листовой меди толщиной 1,5 — 2,5 мм вырезают круг радиусом 60 мм, в центре него размечают место для крепления транзистора и для отверстий под выводы. Затем круг надрезают по радиусу на 12 секторов, которые после крепления транзистора отгибают так, чтобы торцевые плоскости лепестков были под углом 60 — 80° к плоскости крепления транзистора. Поверхность, на которую устанавливают транзистор, должна быть как можно более ровной и очищенной от окислов.
Для обеспечения хорошей передачи тепла от транзистора к радиатору необходимо, чтобы корпус транзистора по всей площади теплового контакта плотно прилегал к радиатору. Наилучшие результаты получаются при хорошей подгонке контактных поверхностей и смазывании их каким-либо невысыхающим маслом, имеющим высокую теплопроводность. Это позволяет снизить тепловое сопротивление контакта транзистор — радиатор в 1,5 — 2 раза. Для транзистора П214 радиатор — звездочка позволяет рассеивать 10 — 15 Вт. Чтобы получить такие же результаты от радиатора в виде сплошного диска (рис. 46,а), необходимо было бы его радиус увеличить до 10 см.
Более эффективно работают радиаторы (заводского изготовления) ребристой или штыревой конструкции (рис. 46,в и г), у которых увеличено отношение теплоотдающей поверхности к общему объему радиатора. Самостоятельно такие радиаторы можно изготовить методом пайки из меди или латуни. В качестве штырей можно использовать отрезки медного провода диаметром 2 — 3 мм, которые тщательно впаивают в пластину толщиной 3 — 5 мм. Рекомендуемый шаг установки штырей 5 — 8 мм.
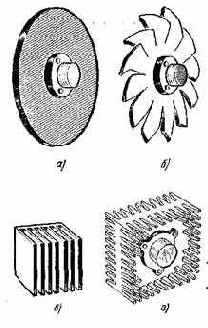
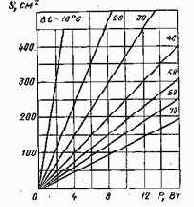
Рис. 46. Радиаторы для мощных полупроводниковых приборов
Рис. 47. График приближенного определения пластинчатого радиатора в зависимости от мощности рассеяния
Для оценки необходимой площади пластинчатого радиатора можно воспользоваться графиком на рис. 47, по которому, зная мощность Р рассеяния транзистора и допустимый перегрев его корпуса по отношению к температуре окружающего воздуха At, можно определить необходимую эффективную площадь 5 поверхности радиатора. Так как S представляет собой сумму площадей лицевой и оборотной стороны радиатора, то для определения размеров сторон (прямоугольной) или радиуса (круглой) пластины в расчет надо подставлять 0,5S. Пластинчатые радиаторы необходимо устанавливать вертикально — только в этом положении их эффективность максимальна.
Заводские радиаторы, которые можно приобрести в магазине, чаще всего делают литыми из алюминиевых сплавов (реже фрезерованными). По эффективности они несколько хуже медных или латунных, зато втрое легче, что и явилось причиной их широкого распространения.
СБОРКА УЗЛОВ КОНСТРУКЦИЙ, ОБРАБОТКА ПОВЕРХНОСТИ ДЕТАЛЕЙ
Для соединения деталей в узел чаще всего используют винты, шайбы и гайки. Винты различают по форме их головки (рис. 48): цилиндрической, полукруглой, чечевицеобразной (полупотайной) и потайной. Цилиндрические винты обеспечивают наиболее прочное соединение, но имеют острые кромки и малопригодны для лицевой панели прибора. Полукруглые головки более красивы и не менее прочны. При использовании винтов обоих типов диаметр отверстия может быть больше диаметра винта, что упрощает сборочные работы (средняя по точности сборка). Винты с полупотайной головкой (особенно хромированные) красивы, но, как и винты с потайной головкой, требуют очень точного выполнения отверстий или установки винтов по месту. Прочность их ниже, чем у винтов с полукруглой или цилиндрической головкой. В соединениях радиоаппаратуры применяют полукруглые винты с низкой головкой большого диаметра — так называемые облицовочные.
Они внешне подобны полупотайным, но гораздо удобнее их для оборки.
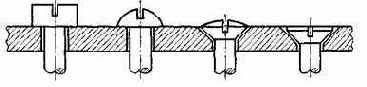
Рис. 48. Виды головок винтов
Шайбы бывают трех видов: нормальные (их наружный диаметр больше диаметра головки винта), подкладные (их наружный диаметр равен диаметру головки винта) и специальные для предотвращения самоотвинчивания винта {шайбы Гровера и звездчатые). Чаще всего радиолюбители используют нормальные шайбы, позволяющие облегчить сборку я закрыть увеличенное отверстие в детали. Нормальные и подкладные шайбы используют для того, чтобы не портить поверхность привинчиваемой детали. Шайбы Лровера и шайбы-звездочки используют тогда, когда изделие работает в условиях значительного перепада температуры, а также механических ударов и вибраций. Конструкция этих шайб препятствует самоотвинчиванию винта.
Гайки изготовляют шта1мповкой и точением. В радиоаппаратуре для упрощения сборки вместо гаек часто применяют нарезание ip-езьбы в металлических элементах конструкции. В последнее время все чаще используют для пластмассовых деталей и деталей из мягких металлов самонарезающие винты, которые при завинчивания сами нарезают для себя резьбу. Их недостаток состоит в том, что они не допускают многократных отвинчиваний и завинчива-«ий, так как резьба легко разрушается.
Штампованные гайки дешевле, но менее надежны. Гайки точеные выпускают нормальной толщины, равной диаметру винта, и тонкие, толщиной до 1/3 диаметра винта. Удобнее в (радиолюбительской практике пользоваться нарезкой резьбы в элементах конструкции, что можно делать даже и в тонких материалах после некоторой вытяжжи материала в отверстие. Конструкции шайб и гаек изображены на рис. 49. В табл. 11 указаны некоторые характеристики резьбовых соединений.
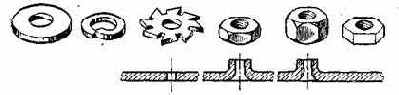
Рис. 49. Виды шайб и гаек (шайба нормальная, шайба Гровера, звездчатая шайба, гайки точеные низкая и высокая, тайка штампованная); формирование резьбы в тонком материале (сверление, вытяжка материала в отверстие и нарезание резьбы)
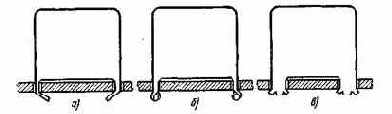
Рис. 50. Крепление деталей отгибкой (а), поворотом (б) и расчеканкой (в) лепестков
Клепкой в радиолюбительской практике чаще всего соединяют детали из алюминиевых сплавов. При этом следует пользоваться алюминиевыми заклепками. Ни в коем случае нельзя для соединения деталей из алюминиевых сплавов, особенно если возможно воздействие влаги, использовать медные заклепки — такое соединение очень быстро разрушается я теряет прочность. Проще всего выполнять клепаное соединение при использовании заклепок с полукруглой головкой, но, чтобы сохранить форму головки, такие заклепки требуют специальной оправки с полусферическим углублением. Для заклепок с потайной головкой необходимо выполнять зенковку отверстия я формовать замыкающую головку. При разборке клепаного соединения заклепку надо просверлить на высоту головки или насквозь с тем, чтобы разрушить закладную или замыкающую, головку и разобрать соединение.
В радиоаппаратуре часто используют соединения металлических деталей с помощью отгибки, поворота и зачеканки лепестков. Примеры таких соединений показаны на рис. 50.
Для получения защитного покрытия хорошего качества на поверхности стальных деталей их необходимо обезжиривать, пассивировать и декапировать. Для обезжиривания можно использовать следующие растворы: сода кальцинированная (или поташ) 100 — 150 г/л и жидкое стекло (силикатный конторский клей) 2 — 3 г/л; сода кальцинированная 20 г/л и хромик 1 г/л. Количество раствора определяется габаритами детали.
Для пассивирования (после которого поверхность металла делается пассивной в электрохимическом отношении) деталь помещают в один из следующих растворов: 5%-ный раствор хромовой кислоты (обработка при температуре раствора 70° С); насыщенный раствор хромпика, 60° С; мыльный раствор, 100° С.
Для декапирования (химического удаления пленки окиси с поверхности детали) используют 5%-ный раствор серной или соляной кислоты. После обработки детали ее необходимо тщательно промыть в проточной воде.
Одно из простейших защитных покрытий стальных деталей — воронение (образование на поверхности детали пленки окисла).
Последовательность выполнения покрытия такова. Деталь шлифуют (если надо, полируют), тщательно обезжиривают и после нагрева до температуры 220 — 325 С° (например, в духовном шкафу с термометром) протирают ветошью, смоченной конопляным маслом. Можно использовать и другие растительные масла, но они дают менее приятный цвет покрытия.
Для получения прочного и красивого лакокрасочного покрытия на поверхности стальных деталей их необходимо тщательно очистить от ржавчины. Для этого деталь помещают в керосин на несколько часов, а затем протирают тканью, обильно смоченной рыбьим жиром, который через 1,5 — 2 ч снимают вместе с ржавчиной. Для быстрого удаления ржавчины рекомендуется в течение нескольких минут промыть деталь в растворе хлорного олова, а затем в теплой воде. Небольшие следы ржавчины удаляют кашицей из толченого древесного угля, замешанного на машинном масле.
После очистки и обезжиривания поверхность детали грунтуют (слой грунта должен иметь толщину не более 0,2 мм, иначе уменьшится прочность лакокрасочного покрытия), а затем окрашивают двумя или более слоями мягкой кистью (движение при нанесении сдоев должны быть в перпендикулярных направлениях) или пульверизатором. Последний способ более удобен радиолюбителю, так как промышленность выпускает много грунтов, лаков и красок в аэрозольной упаковке. Работать с краской в. аэрозольной упаковке следует на открытом воздухе, соблюдая указанные выше меры предосторожности.
Детали из меди и ее сплавов очищают мелкозернистой наждачной бумагой либо кашицей из мелкой поваренной соли с уксусом. Для обезжиривания можно использовать растворы: известь гашеная 35 г/л, едкий галий 10 г/л и жидкое стекло 3 г/л; едкий натр (калий) 75 г/л и жидкое стекло 20 г/л. Деталь помещают в один из этих растворов на 1 ч. Температура должна быть 90° С. Декапируют детали из меди и ее сплавов погружением на 1 мин в 5%-ный раствор серной кислоты.
Для никелирования зачищенную (а еще лучше — отполированную) и обезжиренную деталь помещают в смесь из 10%-ного раствора хлористого цинка и сернокислого никеля, которого должно быть столько, чтобы раствор имел зеленый цвет.
Раствор нагревают до кипения и погружают в него деталь на 1 — 2 ч. Затем деталь переносят во взвесь мела в воде (10 — 15 г мела на стакан) и слегка протирают ветошью, затем промывают в теплой воде и вытирают насухо.
Для серебрения можно воспользоваться отработанным фотофиксажом, в 300 мл которого добавляют 1 — 2 мл нашатырного спирта и 2 — 3 капли формалина. Хранить раствор и работать с ним необходимо только в темноте. Зачищенную, промытую и обезжиренную деталь помещают в раствор на 0,5 — 1,5 ч, после чего промывают в теплой воде, высушивают и протирают мягкой ветошью. Для приготовления описанных выше растворов используют дистиллированную воду либо воду, полученную при оттаивании холодильника.
Детали из алюминия и его сплавов в любительских условиях чаще всего обезжиривают, оксидируют, осветляют и травят. Для обезжиривания пользуются следующими составами: тринатрийфосфат 50 г/л, едкий натр 10 г/л, жидкое стекло 30 г/л; едкий натр 50 г/л. Время обезжиривания первым раствором 2 мин при температуре раствора 50 — 60° С, вторым 3 — 5 мин при 50° С.
Для оксидирования используют следующий состав: углекислый натрий 50 г/л, хромовокислый натрий 15 г/л, едкий натр 2,5 г/л, температура раствора 80 — 100° С, время выдержки в растворе 10 — 20 мин. Обработанную деталь промывают в воде и помещают в кипяток на 15 — 20 мин, вынимают и сушат. Желательно деталь в заключение покрыть бесцветным лаком.
Осветляют алюминиевые детали в растворе буры (50 г/л) с добавлением нашатырного спирта (5 мл/л), которым протирают поверхность детали, а после высыхания деталь протирают ветошью. Детали из силумина (сплава алюминия с кремнием) зачищают, обезжиривают и помещают на 10 — 20 мин в раствор хромового ангидрида (100 г/л) и серной кислоты с удельным весом 1,84 (10 г/л), после чего деталь промывают и сушат.
Весьма надежное и красивое покрытие металлических деталей можно получить, используя бесцветный или подкрашенный клей БФ-2. Клей наносят на поверхность деталей тонким слоем.
Очень часто в радиолюбительской практике приходится обрабатывать органическое стекло. Наиболее прочное окрашивающее покрытие органического стекла получают при использовании красителей, частично растворяющих поверхность детали. В эмалированную или стеклянную посуду наливают цапонлак нужного цвета и погружают в него деталь. Время, необходимое для окраски, может колебаться от 1 с до 15 мин в зависимости от требуемой насыщенности цвета. Чем дольше деталь будет находиться в лаке, тем насыщенней получится окраска. Чтобы получить очень плотное покрытие, деталь погружают в краситель несколько раз, с промежуточной сушкой. Наоборот, если нужно легкое окрашивание, цапон-лак растворяют в любом органическом растворителе.
Детали из органического стекла можно окрашивать анилиновыми красками для фотобумаги. Краску растворяют в укусной кислоте в требуемом соотношении. Раствор пропускают через слой фильтровальной бумаги и смешивают его в соотношении 1 : 1 по объему со следующим составом: толуол — 70% и дихлорэтан — 30%. Полученную смесь фильтруют и растворяют в ней стружку органического стекла в таком количестве, чтобы полученный краситель можно было распылять пульверизатором. На окрашиваемую поверхность краситель наносят в несколько слоев через 10 — 15 мин.
Приготовить краситель можно также следующим образом. Смешивают бензол (60%), дихлорэтан (30%) и уксусную кислоту (10%). В этой смеси растворяют краску. Раствор фильтруют и затем прибавляют в него стружку органического стекла. Окрашивают деталь так же, как и в первом случае, пульверизатором.
Хранить эти красители нужно в хорошо закупоренной посуде (лучше всего с притертой пробкой). Готовить их следует в помещении с хорошей вентиляцией. Как во время приготовления, так и при окрашивании надо остерегаться попадания красителя на руки, лицо, так как пятна очень трудно смыть и, кроме того, он разъедающе действует на кожу.
Чернила для надписей на органическом стекле, винипласте, полистироле, поливинилхлориде и некоторых других пластинках можно сделать из пасты для авторучек, растворенной в дихлорэтане.
Писать можно пером или рейсфедером в хорошо проветриваемом помещении. Надписи стойки к воде.
Не всегда удается достать дихлорэтан для склеивания органического стекла. Заменителем дихлорэтана с успехом может служить клей для кожи, который имеется в продаже в магазинах хозяйственных товаров. Процесс склеивания очень прост: поверхность густо смазывают клеем, соединяют и просушивают под прессом при температуре 30 — 50° С в течение 2 — 3 ч.
Органическое стекло при нагревании легко изгибается, что позволяет применять его для разнообразных конструкций. В качестве примера на рис. 51 показано, как изготовить обойму для элементов 332. Из пластины размерами 86X60 мм вырезают заготовку. Предварительно в пластине нужно просверлить восемь отверстий диаметром 3 мм. Лепестки А и Б заготовки прогрева-вают умеренно горячим утюгом до тех пор, пока органическое стекло не станет мягким, и изгибают вокруг элемента 332, как по шаблону. Затем прогревают остальные лепестки и изгибают их под прямым углом. Контакты для соединения элементов делают из тонкой латунной фольги, загибают на углах и вплавляют в обойму. В готовую обойму средний элемент должен входить с некоторым усилием. Если он входит слишком свободно, следует еще раз прогреть соответствующие лепестки и несколько сблизить их.
Чтобы согнуть под углом относительно большой лист термопластичного материала (органического стекла, полистирола, винипласта), надо на линию сгиба с обеих еторон наложить и прижать две полоски тонкой алюминиевой фольги шириной 1 — 2 см и подключить их к ЛАТРу. Подобрав необходимое напряжение, прогревают место сгиба, снимают фольгу, изгибают лист и удер-живают его в необходимом положении до полного остывания.
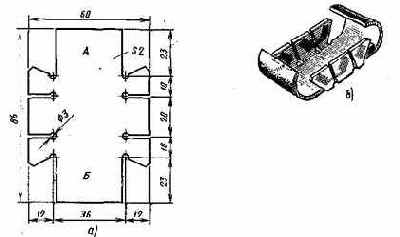
Рис. 51. Развертка (я) и внешний вид (б) обоймы для трех элементов 332 (размеры для справок)
Наиболее доступными видами отделки поверхности деревянных деталей в домашних условиях является воскование, лакирование, окрашивание и оклеивание декоративной пленкой.
Для каждого из этих видов поверхность детали надо тщательно обработать. Основной способ обработки — зачистка наждачной бумагой. Перед последней зачисткой поверхность надо слегка смочнть и потом зачистить сначала поперек волокон древесины, а затем с небольшим на-жимом вдоль волокон. На подготовленную таким образом и хорошо прогретую поверхность можно нанести и втереть тканью тонкий слой светлого воска, который дает приятное матовое покрытие. Оно особенно красиво на поверхности дубовых деталей.
Для лакирования проще всего использовать прозрачные нитролаки, разбавленные до консистенции, при которой их можно распылять пульверизатором. Наносить следует три — шесть слоев лака. Поверхность перед лакированием необходимо хорошо просушить. Окраска поверхности деревянных деталей аналогична окраске металллических.
Часто поверхность детали из древесины тонируют морилками (красителями под тот или иной вид древесины). Вместо морилки «под красное дерево» можно использовать смесь красной и черной туши, подобрав их пропорцию опытным путем. Вместо морилки «под орех» можно использовать аптечный 2%-ный спиртовой раствор йода. Морилку наносят на поверхность древесины вдоль волокон тампоном из ткани, внутрь которого кладут комок ваты. Если однократного покрытия недостаточно, то его повторяют еще раз.
ОГЛАВЛЕНИЕ
Предисловие
Рабочее место радиолюбителя-конструктора
Варианты рабочих мест
Основные требования техники безопасности
Монтажные работы
Материалы для монтажных работ
Инструменты и приспособления для выполнения электромонтажных работ
Намоточные работы
Монтаж деталей на плату и их демонтаж
Слесарные и столярные работы
Материалы для слесарных и столярных работ
Инструменты и приспособления для слесарных и столярных работ
Приемы обработки листовых материалов и древесины
Сборочные и отделочные работы
Приемы компоновки элементов радиоаппаратуры на монтажных платах
Самодельные узлы радиолюбительской аппаратуры
Самодельные радиаторы
Сборка узлов конструкций, обработка поверхности деталей
ББК 32.85
В18
УДК 621.396.6
Редакционная коллегия:
Белкин Б. Г., Бондаренко В. М., Борисов В. Г., Геништа Е. Н., Гороховский А. В., Ельяшкевич С. А., Жеребцов И. П., Корольков В. Г., Смирнов А. Д., Тарасов Ф. И., Хотунцев Ю. Л., Чистяков Н. И.
В18
Варламов Р. Г.
Мастерская радиолюбителя. — М.: Радио и связь, 1983. — 64 с, с ил. (Массовая радиобиблиотека. Вып. 1069).
35 к.
Дается описание работ, выполняемых радиолюбителями при самодельном изготовлении и ремонте радиоаппаратуры. Рассмотрены основные электромонтажные и конструкционные материалы, инструменты для выполнения электромонтажных и механических работ, рабочее место и рациональные приемы обработки, сборки и отделки деталей.
Для широкого круга радиолюбителей.
2402020000-180 ББК 32.85
В--------------87-84
046(01)-84 6Ф2.9
РЕЦЕНЗЕНТ В. Г. БОРИСОВ
Редакция литературы по электронной технике
РЕМ ГЕННАДИЕВИЧ ВАРЛАМОВ
МАСТЕРСКАЯ РАДИОЛЮБИТЕЛЯ
Редактор Л. Н. Ломакин
Редактор издательства Н. В. Ефимова
Художественный редактор Н.С.Шеин
Технический редактор Л. А. Горшкова
Корректор Н. М. Давыдова
ИБ № 859
Сдано в набор 27 06 83 г. Подписано в печ. 13 09.83 г.
Т-18645 Формат 60X90/16, Бумага кн.-журн. Гарнитура литературная Печать высокая Усл. печ. л. 4,0 Усл. кр.-отт. 4,5 Уч.-изд. л. 4,88 Тираж 150 000 экз. Изд. № 19471 Зак. № 76 Цена 35 к.
Издательство «Радио и связь». 101000 Москва, Почтамт, а/я 693
Типография издательства «Радио и связь» Госкомиздата СССР 101000 Москва, ул. Кирова, д 40
Scan Pirat